Linyi Xiangying Wood Based Panel Machinery
Full automatic Thin Calender MDF production line/Thin MDF machinery(1.8-6mm thickness)
Full automatic Thin Calender MDF production line/Thin MDF machinery(1.8-6mm thickness)
Couldn't load pickup availability
Located in Linyi City,Shandong Province,"the Largest Wood BasedPanel Production Base of Asia”,LINYI XIANGYING MACHINERY MANUFACTURING CO.LTD (Linyi Xiangying Machinery Manufacturing Co.,Ltd)is an aggressive manufacturer which specialized in research, development, manufacture and marketing in the field of wood working machines.Since it was established in 1992, Xiangying machinery keeping innovations and perfection to commit themselves in producing best quality machinery.Our main products are Particle board production line,Plywood production line,MDF production line,Melamine laminating product online, etc. Based on our good quality as well as perfect service ,our business scope expands extensively both at home and in more than 20counties such as Vietnam, Malaysia, Pakstan, Bangladesh,Russia,Turkey and so on.And they are all well praised by our clients.Choose Xiangying machinery,Create measureless value.
Continuous roll press thin medium (high) density fiberboard is made of wood fiber as raw material, and processed into a board with a density of 750-880kg /m3 through wood chip preparation section, fiber preparation section, glue supply section, forming prepress section, continuous roll press section and finished product preparation section. The raw materials are wood and branches and ect.
1.Material preparation section
After the raw materials are sawed to wood pieces in certain sizes by wood chipper and stored in material warehouse, clean up the impurities, such as fines, earth and sands, in the wood pieces through screening. The qualified wood chips after screening are sent to the silo for storage by the bucket elevator
2. Fiber preparation section
Feed the wood pieces into the boiling apparatus evenly to cook and soften through squeezing and dewatering after transferring them into the defiberator pre-heating bins/humidifying bins by the transferring equipment in order to separate the fiber easily.The cooked wood pieces will be separated to fibers under the forces of heat and machine. Then mix the wet fibers and heated dry medias ,and keep the fibers suspending in the dry medias under the high speed force of the high-pressure air flow, and the moisture in the fibers will be taken away by the dry media. Afterwards ,the fiber will drop under the force of cyclone separator onto the reversible belt conveyor to be transferred to the pavement bins for temporary storing.
3.Glue dosing system
We adopt first sizing then drying technical process, molten paraffin or other water proof agent directly into the refiner, in the two grinding disk extrusion and rubbing, paraffin evenly mixed with the fiber together. The glue and curing agent are respectively transported to the fiber spray pipe of the refiner under a certain pressure and are fully mixed with the fiber, and the glue mist meets the fiber and adheres to the fiber surface in the drying tank with 28-35m/S high-speed air flow.The system consists of flow sensor, computer control box and speed regulating sizing pump. By continuously adjusting the motor speed of the sizing pump and tracking the theoretical glue amount, the constant ratio of fiber to glue amount is realized.
4.Forming section
The production of high quality thin MDF requires a high quality forming machine, and the mechanical forming machine can meet this requirement. A feeding swing device is located at the upper part of the measuring silo to ensure a consistent fiber height in the width direction. The measuring bin is provided with a rake device in the length direction, which is used to maintain the height of the fiber pile from the measuring bin to the sprinkling roll.
The large-diameter single-head forming roller rotates at high speed, and the fiber is thrown forward along the tangential direction of the rolling roll, so that the structure of the paving slab is even and smooth.
5.Pre-press section
The pre-press we use have has a long feed section and a small inclination Angle, which allows the air in the slab to escape more slowly, otherwise it may cause the fiber on the surface of the slab to blow out and destroy the surface. The fiber slab is compacted by the pressure roller and six pairs of holding rollers, which reduces the rebound of the slab and increases the density and strength of the slab.
In order to monitor the moisture content of the formed slab, the production line is equipped with a high sensitivity online moisture content tester, which can feedback the monitoring results at any time to facilitate process adjustment.
Production of sheet and slab transport is very important. This section uses a belt with a long length, that is, from the exit of the prepress to the entrance of the roller press is completed by a belt conveyor. When there are unqualified slabs, the machine will send the waste slabs to the waste slab recovery system through the movable telescopic belt of the walking trolley.
6.Conti-roller press section
This section is the most important stage of the production line. This equipment organically combines the sections of fiber forming, mats pre-pressing and hot pressing.
The conti-roller press machine is composed of a large diameter hot press roller, two pressure rollers, three guide rollers, pressure steel belt, frame and cleaning roller and ect.
The steel strip is made of high strength stainless steel with a very high finish. In order to ensure that the pressurized steel strip is always running in the middle of the large hot press roll and the guide roll, the pressurized steel strip deviation monitoring device monitors the edge of the belt. Once the deviation is detected, the guide roll at the end of the press machine automatically tilts vertically to adjust.
7.Finish board section
The guide roller of the conti- roller press machine sends the pressed plate to the storage plate frame for cooling, and the cooled mats plate is sent by the traction belt conveyor to the longitudinal sawing edge and the transverse swinging saw for finished sawing treatment. The sawn finished plates are stacked on the hydraulic lifting platform. After the plates are stacked to a certain height, forklifts are used to transport the plates to the finished product warehouse for stacking.
8.Electrical control section
The electronic control system of the production line adopts PLC programmable controller for centralized management, and the display screen of the human-machine interface provides dynamic information of the process state of display and control accuracy. The computer can diagnose the causes of accidents and solutions, and the production line can realize automatic and manual free conversion.
9. Packing
Share





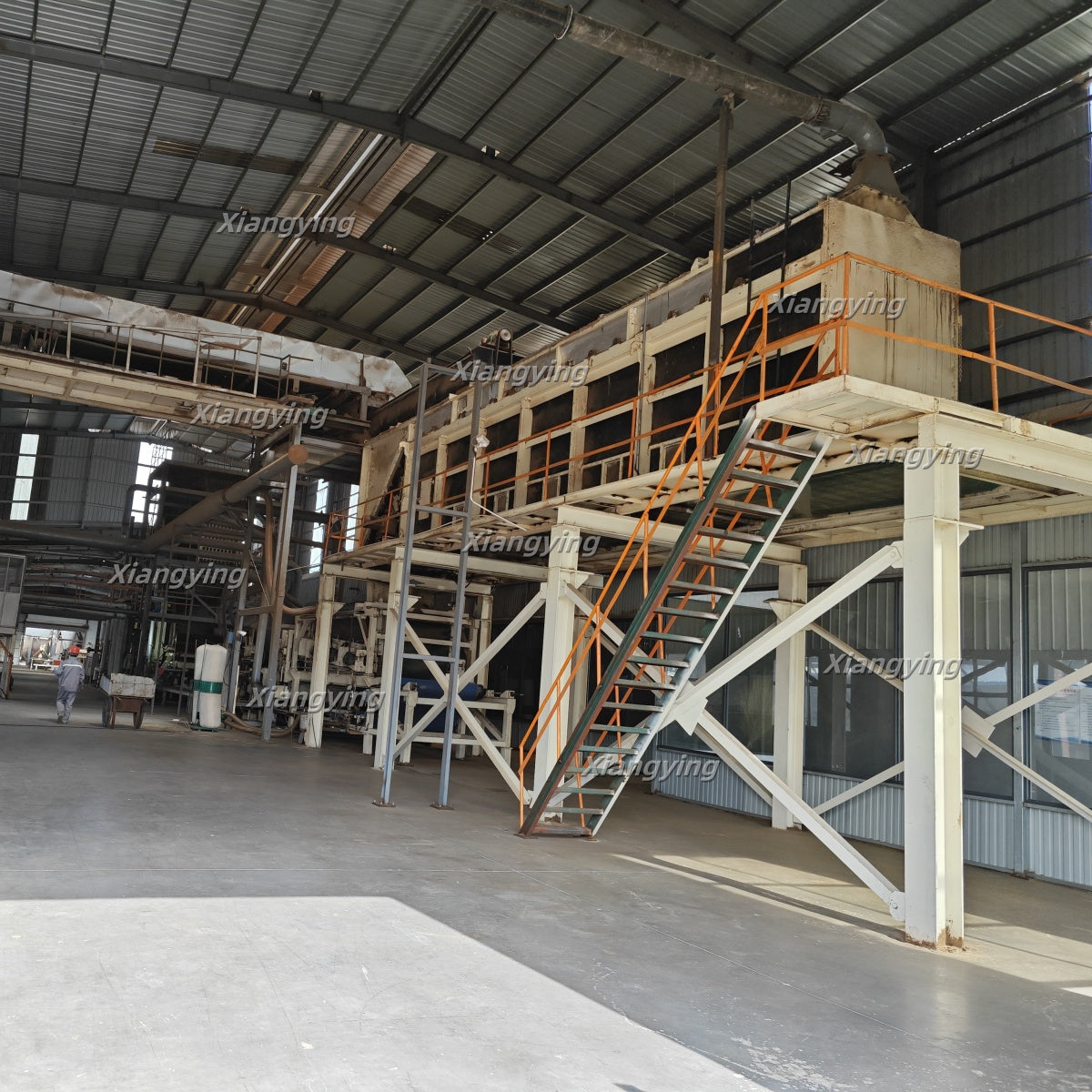
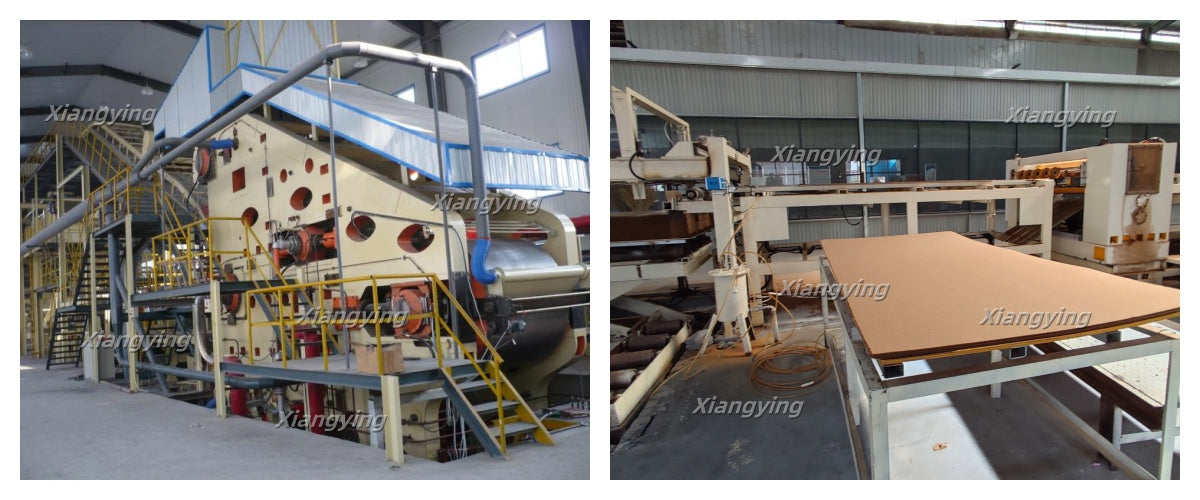
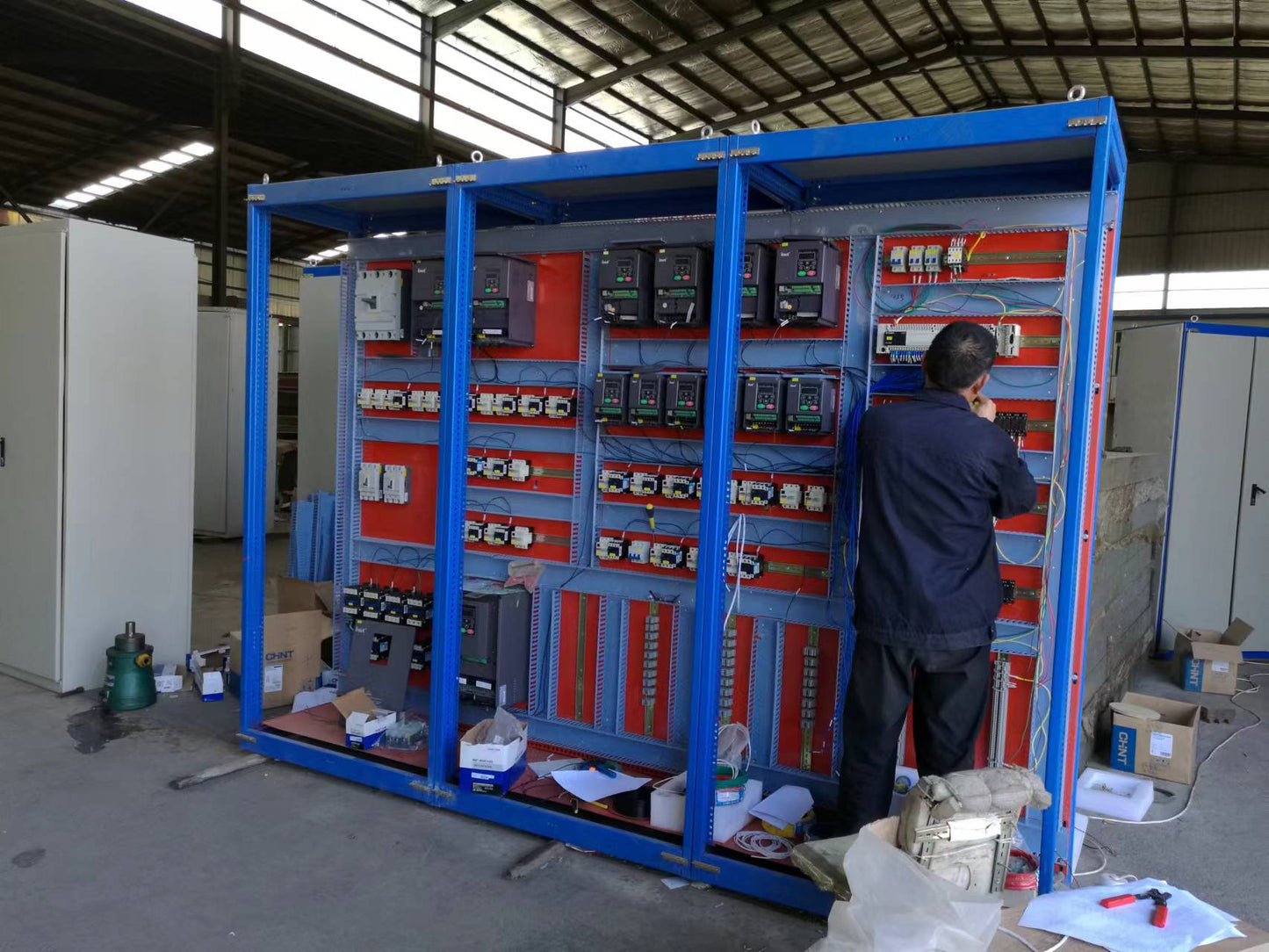